Lockout Tagout (LOTO) programs are designed to protect employees from hazardous energy sources during machine maintenance or servicing. One critical aspect of ensuring a LOTO program remains effective is conducting regular periodic inspections.
Traditionally, these inspections have been time-consuming, requiring manual checklists, observations, and documentation. However, advancements in technology, particularly in software solutions, have transformed how LOTO inspections can be managed. This article explores how modern technology can streamline periodic inspections, reduce errors, and ensure OSHA compliance.
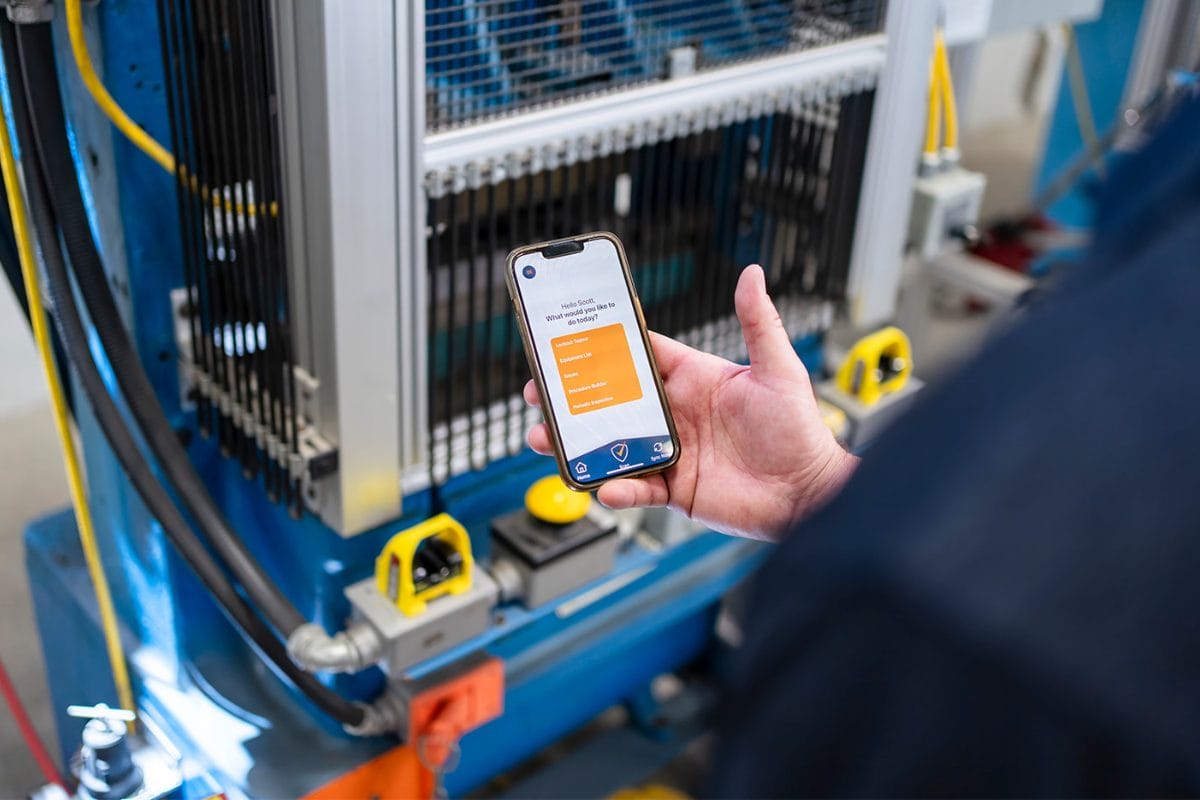
The Importance of Periodic Inspections in LOTO
Periodic inspections are a requirement under OSHA’s 29 CFR 1910.147. Their purpose is to verify the effectiveness of your lockout tagout procedures.
These inspections ensure that employees are following the correct steps, that the procedures themselves are up-to-date, and that any deficiencies are addressed promptly. Without annual periodic inspections, LOTO programs can become outdated, non-compliant, and potentially dangerous.
However, conducting these inspections manually can be labor-intensive, prone to errors, and difficult to document. This is where technology steps in to simplify and enhance the process.
Using Software to Perform Periodic Inspections
One of the best ways to manage a lockout tagout program and stay on top of periodic inspections is by integrating software. Software truly is a tool for success in lockout tagout. Using LOTO software can drastically decrease the time needed to perform lockout tagout procedures or periodic inspections. Not only that, but it can also help with team communication, record keeping, maintaining compliance, and so much more. Due to these advantages, we want to highlight our lockout tagout software, Smart Safety Pro, and how it can revolutionize safety for your company!
Intro to Our Software
Smart Safety Pro software is a mobile app designed for the lockout tagout industry. It is built with the end-user in mind and is meant to simplify and streamline lockout tagout procedures. The goal of integrating software into inspections and safety programs is to help companies and organizations refine their operations, improve compliance, increase efficiency, simplify management, and ultimately to cultivate a safer working environment.
To accomplish these goals, Smart Safety Pro software is equipped with a multitude of purposeful, specialized features. These features are what make SSP the best lockout tagout software available. Now, let’s dive into the top-tier features offered in this product and encover how they can be beneficial in performing loto procedures and periodic inspections.
Premium Features of Smart Safety Pro LOTO Software
Here are the features that make our software stand out from the rest. These features will revolutionize the way that you conduct LOTO procedures and periodic inspections.
Features | Description |
---|---|
Mobile App | Smart Safety Pro’s software can be operated on any device with iOS, Windows, or Android. Because of this, the software can be accessed from virtually any device, including mobile phones, desktop computers, tablets, handheld scanners and more. As a result, workers can carry the technology with them on the job site and use it anytime. This helps users stay updated and situationally aware. |
On-the-Go Reporting | A distinct feature of Smart Safety Pro software is the fact that it doesn’t need wifi to function or update. Lockout tagout procedures can be completed from any mobile device with no data connection required. This enables users to complete LOTO procedures and record them digitally in real time, therefore removing the hassle of papers and filling out reports manually. |
Dynamic Scheduling | Smart Safety Pro software can be used to stay up to date on procedures that need to be done along with upcoming audits. The system will show a countdown for these upcoming events, alerting the users of pending jobs. This feature helps make compliance that much easier, by supporting workers in their efforts to regularly perform LOTO procedures. |
Organized Documentation | SSP software offers a centralized data platform, meaning that all data can be stored in a single place. This helps to keep data organized and easily retrievable in the event of an audit. Within seconds, reports can be pulled up, shared, or printed. |
QR Code Scanning | Our software provides users with a QR code for each set of lockout tagout procedures that coincides with the machinery or equipment it has been developed for. This feature ensures that the right procedures are associated with the right equipment, while also making the procedures easy for authorized users to access. |
Automated Action Triggers | If there are any reported issues during lockout tagout procedures, the system will notify users of needed actions. These notifications encourage a prompt response to issues and help promote safety. Workers and managers alike can see what tasks need to be done and coordinate accordingly. |
There are many other aspects of Smart Safety Pro that make it the ideal lockout tagout app. To learn more about other features, talk to a specialist here.
How Our Software Streamlines the Process
As mentioned before, there are many features of Smart Safety Pro software that make it specialized for lockout tagout. Here are the advantages that come from integrating software into loto operations.
All of these benefits and more are available to those who use Smart Safety Pro software.
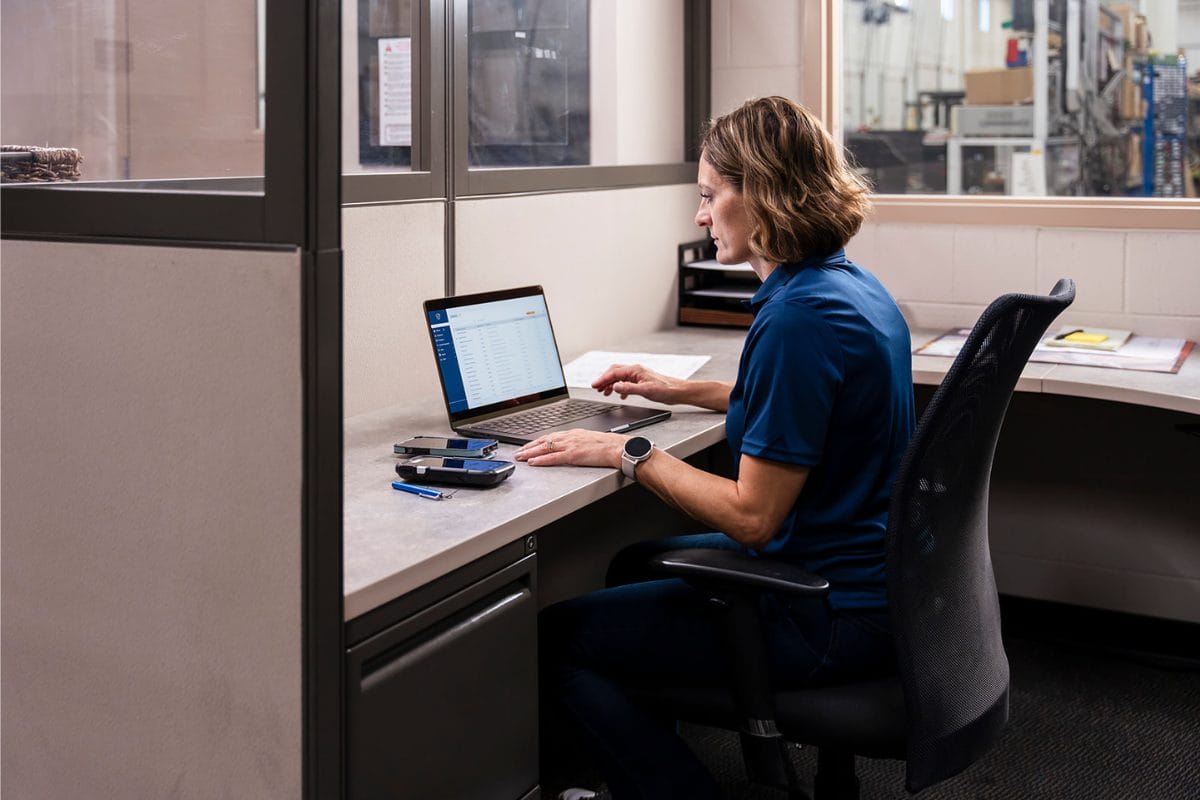
Enhancing Compliance and Accuracy with Technology
In the previous section, we briefly mentioned how software can help with compliance. This section is going to dive into that a bit deeper, since it is such a focus point for companies.
Here’s are 3 prominent ways that technology can enhance compliance efforts:
- Audit-Ready Documentation: Having all inspection reports, corrective actions, and updates stored digitally ensures that you are prepared for any OSHA audit. Software can help you easily fill out reports that detail inspection history, actions taken, and compliance status.
- Reduced Errors: Automation reduces the likelihood of missed steps or incomplete inspections. Digital checklists ensure that all required elements are checked, and the system flags any missing information.
- Consistent Procedures: Software-driven inspections guarantee that employees are following the same procedures each time, preventing inconsistencies that could lead to compliance violations.
Lasting Benefits of Using Technology for Periodic Inspections
Increased Efficiency – Technology significantly speeds up the inspection process by automating repetitive tasks, reducing the need for manual data entry, and providing immediate access to necessary documentation. Inspectors can complete their tasks faster, and managers can spend less time tracking down reports or addressing compliance gaps.
Improved Safety and Compliance – Automating your LOTO inspections ensures that you remain compliant with OSHA regulations, while also improving overall safety. With real-time reporting and corrective actions, safety issues are addressed quickly, reducing the risk of injury or fines.
Cost Savings – While implementing a LOTO software solution may have an initial cost, the long-term savings are substantial. Fewer errors, improved efficiency, and reduced administrative workload all contribute to cost reductions. Additionally, avoiding OSHA fines by ensuring compliance can save significant amounts of money.
Scalability – As your organization grows, your inspection needs will grow as well. Digital solutions are highly scalable, allowing you to expand your inspections across multiple sites or regions without the logistical challenges of manual processes.
Tips for Implementing LOTO Inspection Software
When considering LOTO inspection software, it’s important to keep a few tips in mind:
Invest in Smart Safety Pro Software
Want to learn more about what Smart Safety Pro is and how it can help with lockout tagout? If so, connect with our team by requesting a demo! Our team of specialists are happy to set up a meeting to help you determine if SSP software is right for your company’s needs. We believe in the power of our product to change the way safety is approached in the workplace and want to answer any questions you have. You got a briefing on many of the features of our software in this article, but that was just the beginning! We have a multitude of solution offerings, and hope that you will give us the chance to show just what our lockout tagout software can do!
Conclusion
Technology is revolutionizing how lockout tagout programs are managed, particularly when it comes to periodic inspections. By automating scheduling, streamlining data collection, and providing real-time feedback, LOTO software makes it easier to maintain OSHA compliance, improve safety, and increase efficiency. As organizations increasingly turn to digital solutions, those that adopt LOTO technology will find themselves better equipped to protect their workers and avoid costly non-compliance penalties.
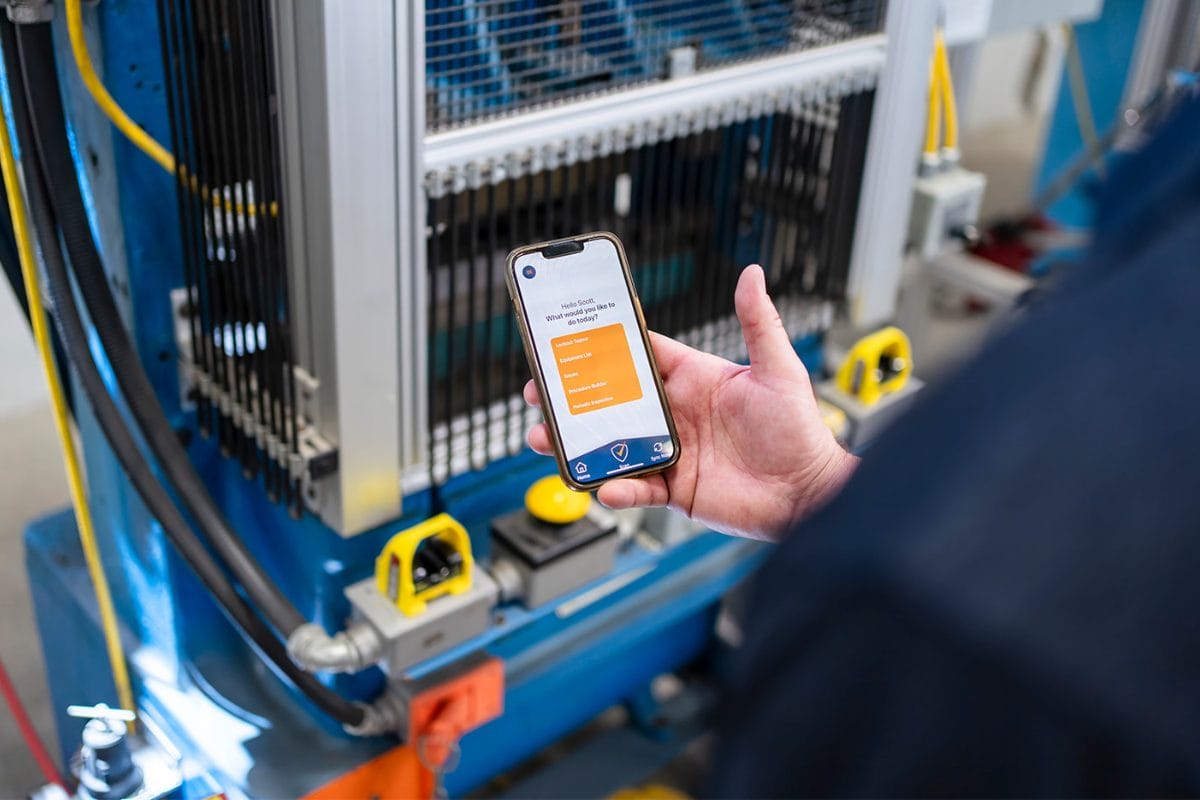